Your cart is currently empty!
Aviation in 2025: Precision, Performance, and Progress
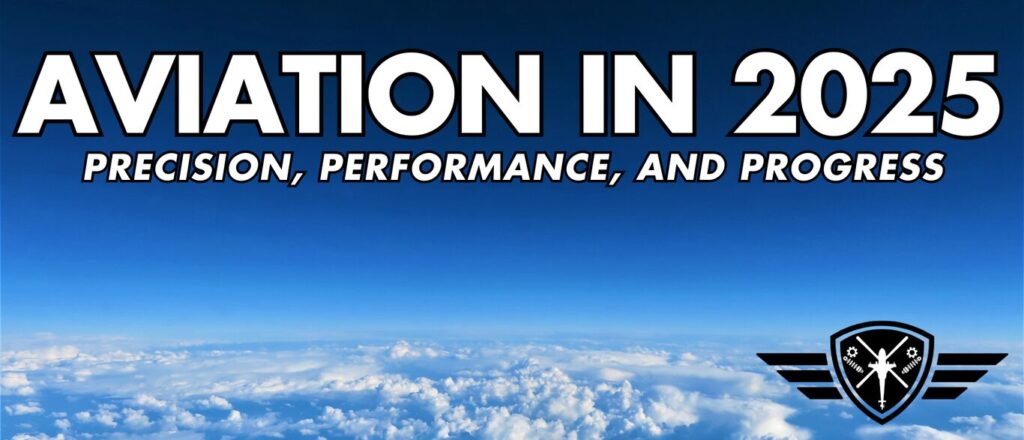
As we step into 2025, the aviation industry continues to push boundaries—delivering not just cutting-edge aircraft but also the vital hardware that ensures safety, reliability, and performance.
At AVBOX US, we’ve been keeping a close eye on trends shaping aerospace hardware to help you stay ahead. These trends may be driving innovation, but the foundational components—AN, NAS, and MS parts and hardware remain indispensable for maintaining today’s aircraft and ensuring their safe operation.
1. Sustainability Takes Flight
Sustainability in aerospace hardware is no longer optional, it’s essential. With mounting environmental concerns and stricter regulations worldwide, airlines and manufacturers are rethinking how they design, source, and produce hardware components.
- Lifecycle Analysis Standards: Traceability is key. Manufacturers are increasingly required to perform lifecycle analyses (LCA) on parts to ensure sustainability from production to recycling. This includes sourcing raw materials responsibly, minimizing waste during production, and ensuring parts can be safely disposed of or recycled at the end of their lifecycle.
- Green Manufacturing Practices: Aerospace suppliers are integrating green energy solutions, such as solar-powered production lines and advanced waste management systems, to meet sustainability targets. Companies adopting these practices not only comply with regulations but also attract eco-conscious customers.
- Eco-Friendly Materials: Advanced materials like lightweight composites, recycled alloys, and bio-based polymers are becoming mainstream. These materials reduce overall aircraft weight, leading to better fuel efficiency and lower emissions, a win-win for performance and sustainability.
2. Digital Transformation in Supply Chains
Digital transformation is reshaping the way aerospace hardware is manufactured, tracked, and certified. In an industry where precision is critical, the adoption of advanced technologies ensures parts are delivered on time and meet stringent safety and quality standards.
- Smart Hardware Tracking: RFID and QR-coding systems enable real-time tracking of individual parts throughout the supply chain. Maintenance teams can now scan a part to access its entire history, including manufacturing details, certifications, and previous installations.
- Blockchain for Certification: Blockchain technology is revolutionizing the way aerospace certifications are handled. By storing certifications and part history on an immutable ledger, manufacturers and suppliers can ensure the authenticity of parts, reducing counterfeiting risks and streamlining compliance audits.
- Predictive Analytics: Using AI and machine learning, aerospace companies can now forecast demand for specific hardware components with remarkable accuracy. Predictive maintenance, enabled by these tools, also reduces unexpected aircraft downtime, leading to significant cost savings.
3. Rising Demand for Precision and Performance
As aircraft designs become more advanced, the demand for precision-engineered hardware continues to grow. Aerospace components must not only meet but exceed performance expectations in extreme environments.
- High-Temperature Alloys: Jet engines and other high-stress components rely on alloys that can withstand extreme heat and pressure. Nickel-based superalloys and other advanced materials are seeing increased use, especially in cutting-edge propulsion systems for commercial and military aircraft.
- Micro-Tolerance Fasteners: Modern aerospace designs demand fasteners with near-zero tolerances to ensure perfect fit and structural integrity. This is particularly important in next-generation aircraft, where even the smallest deviations can impact aerodynamics and fuel efficiency.
- Customization: Original Equipment Manufacturers (OEMs) are requesting more bespoke hardware to meet specific performance requirements. From fasteners designed for high-vibration areas to lightweight brackets for electric aircraft, customization is a driving innovation in the industry.
4. The Growth of Urban Air Mobility (UAM)
The future of transportation is taking to the skies, with Urban Air Mobility (UAM) emerging as a rapidly growing sector. UAM refers to the development of new aircraft, including electric vertical take-off and landing (eVTOL) vehicles, designed for short-distance transportation in urban environments. These innovations promise to revolutionize commuting, cargo delivery, and even emergency response systems.
It’s a vision of the future that feels straight out of Back to the Future II—though instead of a DeLorean zipping through the sky, we’re looking at sleek, battery-powered eVTOLs ready to beat traffic.
- Lightweight Standards for Efficiency: UAM vehicles demand hardware that balances minimal weight with maximum strength. Every gram matters when optimizing energy use, especially in battery-powered designs where weight directly impacts range and efficiency. Advanced materials like titanium alloys and carbon composites are becoming industry staples.
- Battery and Power System Integration: Unlike traditional aircraft, UAM vehicles rely on advanced battery technology. Hardware components must seamlessly integrate with high-voltage power systems, ensuring safety and durability in high-energy environments.
- Applications Beyond Commuting: While reducing urban congestion is the most publicized benefit of UAM, its applications extend into logistics, healthcare, and emergency response. From delivering packages to transporting medical supplies, UAM is poised to reshape industries beyond passenger travel.
- Rapid Certification Processes: The Federal Aviation Administration (FAA) and the European Union Aviation Safety Agency (EASA) are working with manufacturers to streamline certification for UAM-specific components.
"The FAA is committed to working with industry leaders to safely integrate Urban Air Mobility into our national airspace, ensuring a scalable and sustainable framework for this revolutionary form of transportation.”
Urban Air Mobility (UAM) Concept of Operations
5. The Timeless Role of AN, NAS, and MS Parts in Modern Aviation
While Urban Air Mobility (UAM) and other forward-looking innovations dominate the headlines, it’s critical to remember that much of the aviation industry relies on the proven standards of AN, NAS, and MS hardware. These parts have been the backbone of aviation maintenance and repair for decades and will remain essential for years to come.
- Supporting Current Fleets: With thousands of models of aircraft in operation globally, from commercial airliners to military fleets, AN, NAS, and MS parts are critical for routine maintenance, overhauls, and repairs. These components are designed to meet rigorous standards, ensuring the safety and reliability of existing aircraft.
- Compliance and Standardization: AN, NAS, and MS parts represent decades of engineering expertise and standardization, making them the gold standard for compatibility and compliance. They are widely accepted across the aviation industry, ensuring seamless sourcing and integration.
- Innovation Builds on Proven Foundations: While emerging technologies like lightweight composites and advanced alloys are expanding what’s possible, innovation doesn’t replace foundational components—it enhances them. Future aircraft designs will likely integrate these newer materials alongside traditional parts, creating hybrid systems that draw on the strengths of both.
At AVBOX US, we recognize the enduring value of AN, NAS, and MS hardware. These components are not only vital for maintaining current aircraft but also play a supporting role in the transition to next-generation aviation.
How AVBOX US Is Preparing for 2025
At AVBOX US, we pride ourselves on staying informed on these trends to better serve our customers. Whether you’re sourcing high-performance parts for the latest innovations or the trusted AN, NAS, and MS components that keep fleets operational, we’re your wingman the entire way.
Leave a Reply
You must be logged in to post a comment.